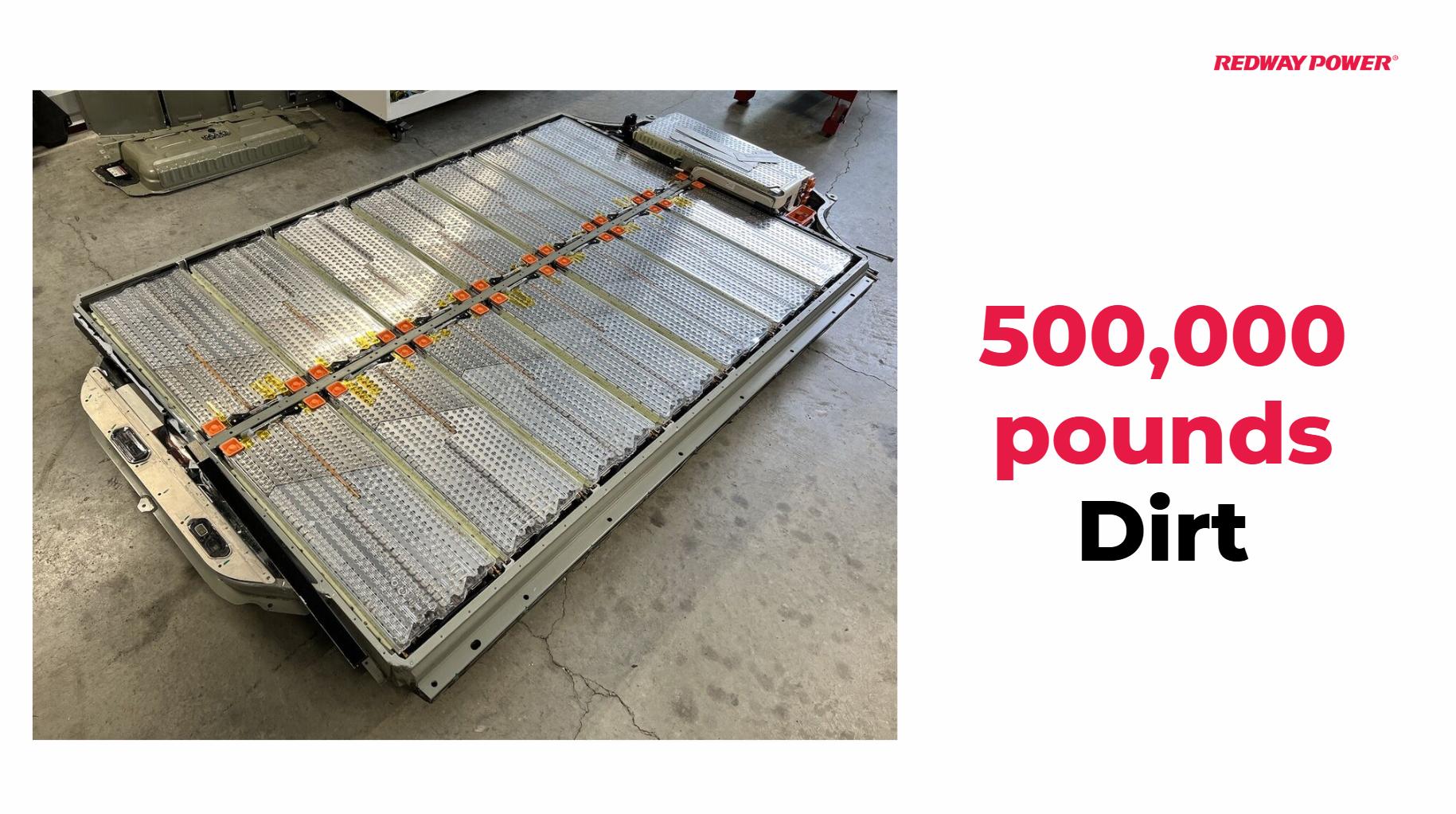
How Much Dirt Is Moved to Make a Tesla Battery?
The production of a Tesla battery involves significant amounts of raw materials, which translates into moving large quantities of dirt during the extraction process. On average, it takes about 500,000 pounds of earth to produce a single electric vehicle battery, highlighting the environmental impact of battery manufacturing.
How Is Dirt Moved During the Production of Tesla Batteries?
The process of producing lithium-ion batteries for electric vehicles like those made by Tesla begins with mining raw materials. This involves large-scale excavation where significant amounts of earth are moved to extract essential minerals such as lithium, cobalt, nickel, and graphite. For every battery produced, hundreds of thousands of pounds of soil and rock must be processed to obtain these materials.
Chart: Estimated Earth Moved for Raw Material Extraction
Material | Estimated Dirt Moved (lbs) per Battery |
---|---|
Lithium | 200,000 |
Cobalt | 150,000 |
Nickel | 100,000 |
Graphite | 50,000 |
Total | 500,000 |
What Raw Materials Are Required for Tesla Batteries?
Tesla batteries primarily require several key materials:
- Lithium: Essential for energy storage.
- Cobalt: Stabilizes battery chemistry.
- Nickel: Enhances energy density.
- Graphite: Used in anodes.
These materials are crucial for the performance and longevity of lithium-ion batteries.
Why Is the Extraction Process Significant for Battery Production?
The extraction process is significant because it directly impacts both the supply chain and environmental sustainability. The mining operations required to obtain lithium and other materials can lead to habitat destruction, water depletion, and pollution. Understanding these impacts is vital as demand for electric vehicles continues to rise.
How Does Tesla’s Manufacturing Process Impact Environmental Sustainability?
Tesla is actively working to improve the sustainability of its battery production through innovations such as dry electrode technology. This method reduces water usage and minimizes waste compared to traditional wet processes. By optimizing production efficiency, Tesla aims to lessen its environmental footprint while meeting growing demand.
Chart: Environmental Impact Comparison
Method | Water Usage (Liters) | Waste Produced (kg) |
---|---|---|
Traditional Wet Process | 1000 | 200 |
Dry Electrode Process | 100 | 50 |
What Are the Challenges in Scaling Up Battery Production?
Scaling up battery production presents several challenges for Tesla, including:
- Technological hurdles: Perfecting dry electrode technology at mass scale remains complex.
- Supply chain issues: Securing consistent access to raw materials is critical.
- Production capacity: Meeting ambitious production targets requires significant investment in facilities and equipment.
These challenges must be addressed to fulfill market demand efficiently.
How Much Dirt Is Actually Involved in Making One Tesla Battery?
In total, approximately 500,000 pounds of dirt are moved to produce a single Tesla battery. This figure encompasses all raw materials needed for the manufacturing process, emphasizing the extensive mining operations required to support electric vehicle production.
Industrial News
Recent developments indicate that Tesla is ramping up efforts to enhance its battery production capabilities amid increasing demand for electric vehicles. The company is focusing on improving its dry electrode technology while addressing supply chain challenges related to lithium and cobalt sourcing. As global interest in EVs grows, manufacturers are under pressure to innovate sustainably and efficiently.
Lithium Battery Expert Views
“While the demand for electric vehicle batteries continues to soar, we must not overlook the environmental costs associated with raw material extraction,” says Dr. Sarah Thompson, a leading expert in sustainable energy solutions. “Tesla’s advancements in dry electrode technology are promising steps toward reducing these impacts but require ongoing commitment and innovation.”
FAQ Section
How much dirt is moved to make one Tesla battery?
A1: Approximately 500,000 pounds of dirt is moved during the production of a single Tesla battery.
What are the main raw materials used in Tesla batteries?
A2: The primary raw materials include lithium, cobalt, nickel, and graphite.
Why is mining significant for battery production?
A3: Mining is significant because it affects supply chains and has substantial environmental impacts.
How does dry electrode technology improve sustainability?
A4: Dry electrode technology reduces water usage and waste compared to traditional methods.
What challenges does Tesla face in scaling up battery production?
A5: Challenges include technological hurdles, supply chain issues, and meeting production capacity targets.